- News
26 June 2013
Cambridge Nanotherm delivers first order for its Chip-on-Heatsink technology in partnership with Optocap
In partnership with contract microelectronic and optoelectronic packaging design & assembly firm Optocap Ltd of Livingston, Scotland, UK, Cambridge Nanotherm Ltd of Haverhill, UK says that the first commercial order for its Chip-on-Heatsink modules have been shipped to a customer in the LED industry.
“As a design and assembly service provider we need to ensure we specify materials that will enhance our customers’ products,” says Optocap’s CEO David Ruxton. “We specified Cambridge Nanotherm’s technology due to the outstanding thermal performance it enables,” he adds. “It also means a reduced bill of materials, simplified supplier management and easier assembly for our customer.”
Established in 2010 to commercialize proprietary nano-ceramic technology for the electronic industry, Cambridge Nanotherm was supported by grants from the UK’ Technology Strategy Board (TSB), East of England Development Agency (EEDA) and European Regional Development Fund (ERDF) and was a member of the Carbon Trust Fast-track Entrepreneur Programme. Since 2011 it has been financially backed by Enso Ventures. The firm was the UK winner of the 2011 Clean Tech Open Competition, sponsored by Silicon Valley Bank.
Cambridge Nanotherm’s core IP is a unique process for converting aluminium into alumina. The process allows the surface of any aluminium object to be converted into a dielectric layer. In the case of the Chip-on-Heatsink approach, an extruded heat-sink or heat-pipe can be coated and then metallized with the end-user’s circuit design. Nanotherm’s technology enabled Optocap to utilize its advanced manufacturing processes, allowing direct assembly of die and surface-mount components onto the heat-sink, creating a fully integrated module.
For LED lighting customers using conventional PCB materials and heat-sinks, the advantages are three-fold: (1) a cost reduction is seen through the removal of both the MCPCB and thermal interface material (TIM) components; (2) the removal of these layers gives the most efficient thermal path between component and heat-sink; and (3) as a result of minimizing thermal resistance, denser component layouts can be realised. For those using thick-film or thin-film metallized alumina and aluminium nitride ceramic heat-sinks, the cost reduction is even more significant, while bulk thermal performance of the aluminium heat-sink matches one made from aluminium nitride.
“We are very pleased to have Optocap as the world’s first commercial customer for the first ever Chip-on-Heatsink product,” says Cambridge Nanotherm’s CEO Dr Pavel Shashkov. “Working with Optocap we were able to demonstrate that our product has clear technological advantages as well as real commercial benefits,” he adds. “We believe that this technology will change the rules of the game for manufacturers not just in the LED field but in the electronics industry as a whole.”
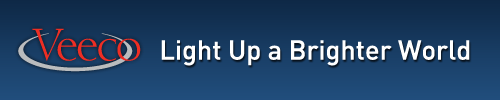